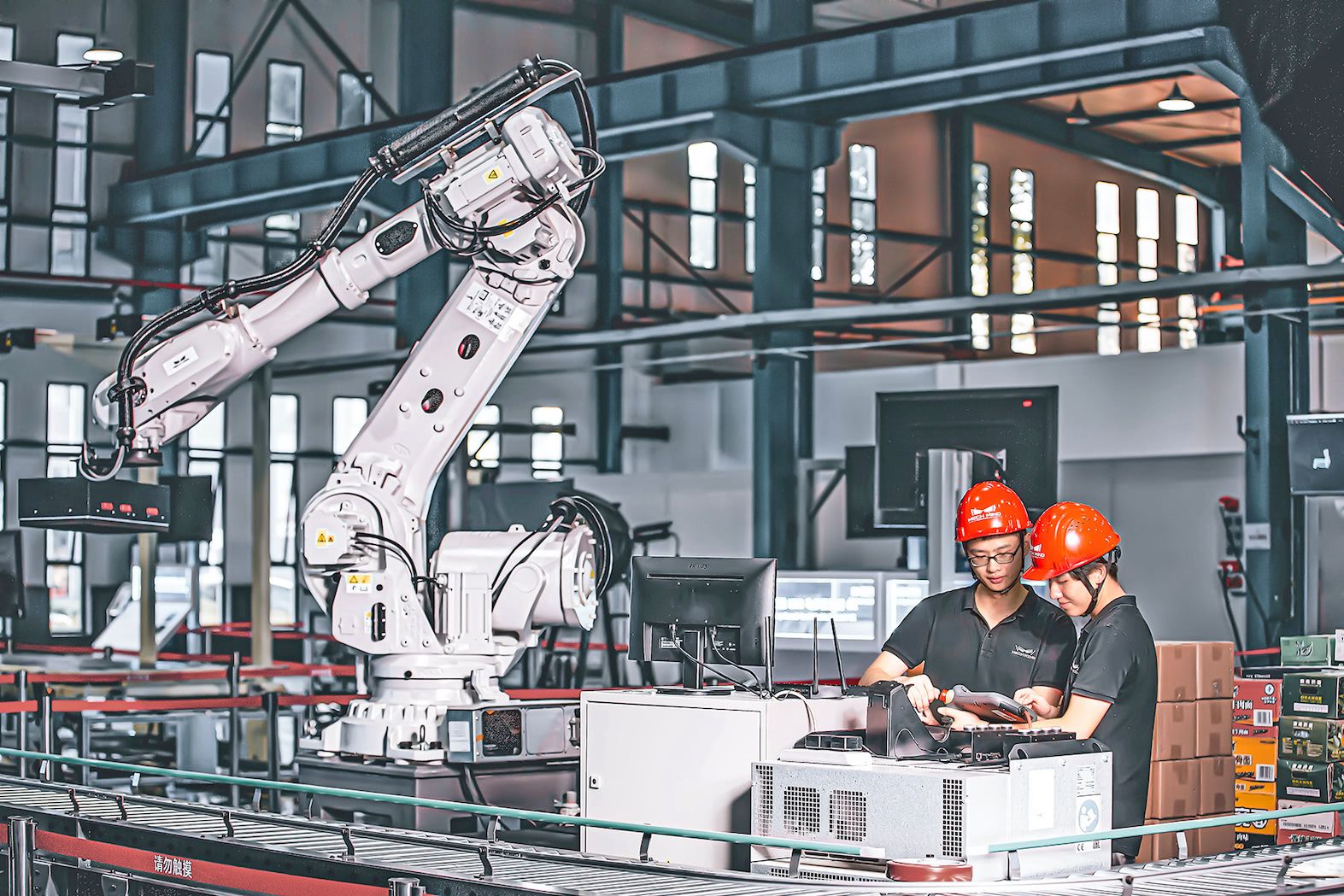
TWI – Standardizzazione e diffusione della conoscenza: il caso di un'azienda italiana
Un "case study" di una multinazionale italiana dell'automotive. I risultati del TWI (Training Within Industry) ad un mese dall'intervento.
Un tipico luogo comune è che la standardizzazione sia una metodologia adatta ad aziende labour intensive, che prevedono operazioni di assemblaggio o comunque a forte contenuto manuale. In realtà anche in un’azienda di processo a forte componente capital intensive, le performance complessive non possono prescindere dalla capacità degli operatori di eseguire correttamente le loro attività.
Non è sufficiente dotarsi di impianti all’avanguardia per garantire al cliente qualità, costi e servizio. È necessario sviluppare standard operativi efficaci, e soprattutto, insegnare agli operatori come applicarli correttamente.
Il Training Within Industry (TWI) è il metodo che l’azienda, una multinazionale “italiana” nel settore della componentistica automotive, ha adottato per rinforzare la standardizzazione dei processi, diffondere conoscenza e abilità, velocizzare l’apprendimento dei nuovi assunti e migliorare le performance operative.
In questo “case study” vedremo come è stato possibile ridurre i reclami cliente del 100%, le difettosità interne del 96% e il tempo di formazione di un neo-assunto da alcuni mesi a soli 30 minuti, e tutto questo a un solo mese dall’intervento.
Il Contesto
L’azienda, con un fatturato che supera i 700 Mln€ e più di 4000 dipendenti in 12 stabilimenti, è un gruppo industriale attivo nella produzione di componenti per i principali OEM Automotive, truck, movimento terra, agricolo, marino.
L’azienda opera da anni adottando metodi e strumenti della Lean Production e ha creato una struttura dedicata alla formazione continua: l’Academy interna. Questa ha lo scopo di addestrare efficacemente gli operatori e diffondere sempre di più la cultura del Lean management.
Per ogni divisione sono state create strutture ad hoc e programmi formativi specifici, con l’obiettivo di diffondere in maniera sempre più capillare gli strumenti ed in generale la cultura Lean e del miglioramento continuo.
Nell’ambito di questi progetti formativi l’azienda ha visto nel TWI una metodologia efficace per migliorare la standardizzazione delle proprie operazioni e soprattutto per favorire lo sviluppo delle tre principali abilità di un buon “supervisore”:
- abilità ad istruire
- abilità a migliorare
- abilità a guidare
Volendo essere sicuri di una corretta ed efficace applicazione del metodo, che è stato alla base del successo e dello sviluppo del Toyota Production System, l’azienda si è rivolta all’unico organismo internazionale in grado di fornire garanzia e certificazione di corretta applicazione: il TWI Institute.
Grazie al supporto di Fabrizio Paolin, referente italiano dell’istituto e Certified Master Trainer, è stato lanciato un programma di applicazione del TWI in azienda ad iniziare dal modulo Job Instruction.
Il Bisogno
Pur non essendo l’azienda digiuna di strumenti e di tecniche appartenenti al Lean Management sentiva il bisogno di migliorare la standardizzazione delle proprie operazioni.
Il progetto di applicazione del TWI ha voluto quindi dare una risposta ad alcune criticità che si stanno vivendo:
- La mancanza di un metodo standard di addestramento sulle operazioni critiche genera, da un lato un tempo di “onboarding” troppo lungo che a sua volta si traduce in costi di affiancamento e/o in perdite di efficienza e dall’altro problemi di qualità.
- Il mancato rispetto degli standard in operazioni critiche genera difetti nel prodotto che provocano scarti e rilavorazioni, con conseguente allungamento del lead time e aumento del costo di produzione. Inoltre, se il difetto non viene rilevato dall’azienda, verrà notato dal cliente danneggiando il brand e mettendo a repentaglio le vendite.
Il modulo Job Instruction del training Within Industry è la risposta più adeguata a questi problemi frequenti in azienda.
Il metodo: cos'è il TWI
Il Training Within Industry (TWI) è un metodo molto pratico che permette di gestire con successo i problemi che ogni giorno si verificano in azienda, e che rendono difficile l’applicazione e il rispetto degli standard, e instabili i nostri processi.
Si fonda sul principio che i capi intermedi giocano un ruolo fondamentale nel quotidiano mantenimento (e miglioramento) degli standard e nel raggiungimento degli obiettivi aziendali.
Per fare ciò essi debbono possedere alcune abilità fondamentali:
- abilità a insegnare rapidamente ai propri uomini come fare il lavoro nel modo giusto (standard work)
- abilità a coinvolgerli e a guidarli verso gli obiettivi aziendali (leadership)
- abilità a trovare sempre un modo migliore per fare il lavoro (miglioramento continuo)
All’interno del TWI sono stati sviluppati 3 percorsi specifici per insegnare queste tre abilità:
- JI – Job Instruction
- JR – Job Relations
- JM – Job Method
Dotare i propri capi intermedi di queste abilità significa promuovere in azienda la stabilità, sviluppare il vero standard work, creare una forte cultura del miglioramento sostenibile e insegnare il “Rispetto per le persone”.
L’approccio “tradizionale” della gestione dell’apprendimento era caratterizzato dall’imparare dai tentativi/errori, dall’autogestione dell’apprendimento e l’affiancamento era “Sistema del compagno”. Al contrario, il TWI favorisce lo sviluppo di una forza lavoro più produttiva attraverso lo sviluppo di attività di training sul luogo di lavoro con le seguenti caratteristiche:
- è “people centric” e focalizzato sullo sviluppo delle abilità;
- tiene in considerazione le caratteristiche del singolo e del team;
- dà molta importanza all’ambiente di formazione e alla cultura della collaborazione;
- guida il sistema verso la stabilizzazione, standardizzazione e poi il miglioramento.
Possiamo quindi affermare che il TWI è un metodo per consolidare la standardizzazione e capitalizzare la conoscenza.
L'Attività pilota
Come in tutti i progetti di cambiamento anche in questo caso si è iniziato dal una serie di esperienze pilota, per acquisire confidenza con il metodo e per misurare i vantaggi che ne derivano.
Sono state lanciate quindi tre azioni pilota in tre differenti stabilimenti, con l’obiettivo di validare il metodo, ma anche di ottenere da subito importanti miglioramenti di performance.
1– Il primo esempio riguarda uno degli stabilimenti esteri, dove si producono scatole cambio. Qui è stato realizzato un percorso completo di adozione della metodologia Job Instruction (training e coaching-followup) coinvolgendo un team interfunzionale composto dagli Shift Leaders, responsabili delle linee di produzione di alcune parti ben identificate (destinate al cliente in questione), dai responsabili dell’OPEX di stabilimento, dai Quality Inspectors specializzati in quei Part Numbers e da alcuni rappresentanti della Corporate Academy.
Il focus dell’intervento ha riguardato i processi di Visual Inspection interni, per i quali gli standard erano carenti, e gli operatori (Checker) non conoscevano o non seguivano stabilmente gli standard, generando reclami da parte del cliente. Per rimediare a questi l’azienda, su espressa indicazione del cliente, si era dovuta dotare di una sovrastruttura esterna di ispettori (firewall), sopportandone anche i relativi costi, che comunque non riusciva a garantire un filtro efficace al 100%.
2– Il secondo esempio riguarda uno stabilimento italiano dove l’esigenza era quella di velocizzare l’introduzione dei nuovi operatori nelle linee di produzione. In questo caso si trattava di processi produttivi lunghi ed articolati e che richiedevano l’impiego di grandi linee composte da più macchine utensili. Per questo le attività assegnate agli operatori erano a volte piuttosto complesse e, prima dell’introduzione di Job Instruction, richiedevano lunghi tempi di training per permettere ai nuovi arrivati di svolgerle
autonomamente senza errori e nei tempi assegnati.
3– Il terzo esempio di progetto pilota, è stato realizzato in un altro stabilimento estero anch’esso specializzato nella produzione di scatole cambio, ed ha riguardato l’addestramento di nuovi operatori nella realizzazione di attività simili a quelle effettuate nel primo progetto pilota, e relative all’ispezione di alcune specifiche parti. Anche in questo caso l’utilizzo dello strumento dei JBS (Job Breakdown Sheet) per ognuna delle famiglie di prodotti coinvolte ha permesso di scomporre in fasi, analizzare e identificare la corretta sequenza di operazioni e standardizzare il processo ispettivo.
In tutti e tre i progetti pilota durante le fasi di scomposizione del lavoro, e di ricerca dei punti chiave di ciascuno dei passi che li componevano, il coinvolgimento diretto degli Shift Leaders e degli altri attori (Opex e QI), ha favorito lo sviluppo di numerose proposte di miglioramento che hanno condotto ad identificare nuovi e più efficaci standard.
I primi risultati
Su tutti e tre i progetti pilota si sono raggiunti ottimi risultati in tempi molto brevi:
- Primo progetto pilota: a partire da una situazione iniziale media nella prima parte del 2020 di 3-5 reclami cliente al mese e di 25 difetti/giorno bloccati dalla funzione di “internal firewall”, dopo aver effettuato il training nella settimana 40 e il follow-up nelle settimane 41, 42 e 43, si è giunti alla situazione di 0 (ZERO) reclami cliente e 8 difetti/giorno a partire dalla settimana 49; sempre 0 (ZERO) reclami e 1-2 difetti/gg nella settimana 2/2021 e l’obiettivo di eliminare le attività di “internal firewall” entro la fine di gennaio 2021.
- Secondo progetto pilota: 30 e 45 minuti (a seconda della tipologia di macchina utensile e del task assegnato) è il tempo medio di formazione per insegnare come effettuare correttamente operazioni base di carico e scarico di una macchina o di assemblaggio di un sottogruppo; in altre parole, per operare in autonomia da parte di operatori neo assunti. Dopo una settimana dall’istruzione, è stata effettuata la verifica di quanto gli operatori ricordavano dell’istruzione ricevuta, ed il risultato è stato sorprendente: 96,7% in un caso e 91,7% nell’altro.
- Terzo progetto pilota: il test che riguarda la rilevazione del livello di ripetitività delle attività del processo di analisi della qualità, sul quale le persone erano state formate, dopo una settimana ha fornito un risultato dell’86% sul primo operatore formato, e del 100% sul secondo operatore formato, con valore minimo atteso per il superamento del test pari al 70%. Dopo due settimane dalla formazione il test, come da standard, è stato ripetuto ed ha dato un esito positivo al 100% in entrambi i casi, come da valore atteso.
Prossimi passi
L’azienda con queste tre esperienze pilota ha potuto convalidare l’affidabilità e l’efficacia del metodo TWI, ma soprattutto ha potuto verificare direttamente i miglioramenti di performance che si possono ottenere, per cui ha deciso di lanciare un programma più vasto di applicazione del modulo Job Instruction, e di puntare in futuro sulla diffusione e sull’applicazione di tutti e tre i moduli del Training Within Industry.
Conclusioni
Oggi molte aziende hanno a disposizione strumenti sofisticati ed impianti performanti, ma i risultati dei processi produttivi non possono prescindere dalla disponibilità di processi stabili, standardizzati e di una forza lavoro in grado di applicare e migliorare continuamente tali standard.
Al crescere della complessità degli impianti e delle aspettative di mercato, aumenta la necessità di avere operatori formati, sicuri e veloci. Il Training Within Industry deve essere considerato come uno strumento di base nel percorso verso l’eccellenza operativa.